The Warehouse Safety Checklist: 9 Steps to a Safer Warehouse Environment
Article published on Apr 10, 2018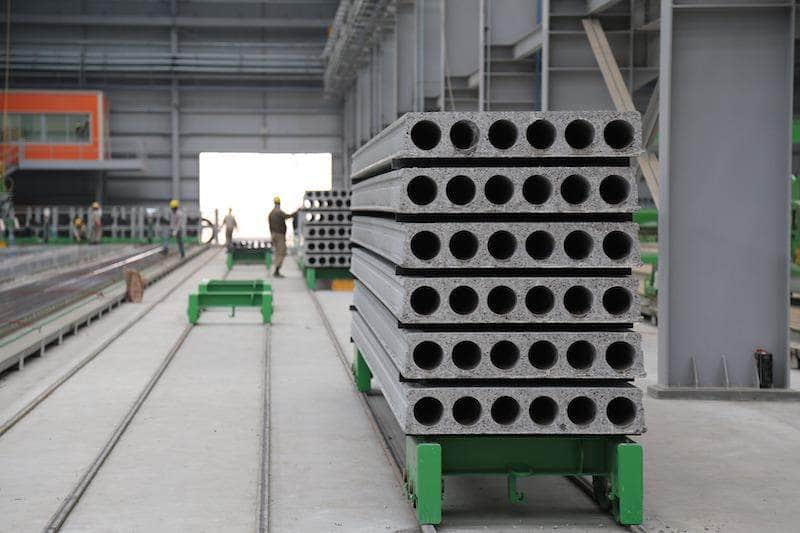
According to the Bureau of Labor Statistics, over 3 million accidents occur in the workplace every year.
Nearly half of those accidents occur in warehouses, costing warehouse owners over $1,000,000,000 in workers compensation costs every year.
In warehouse environments, safety procedures are often overlooked because of tight schedules, inadequate resources, or because safety procedures are seen as a way to cut corners and save some money.
But unsafe warehouses can lead to a number of entirely preventable workplace injuries, accidents, safety violations, and fines from the Occupational Safety & Health Administration (OSHA).
How do you avoid warehouse injuries and keep your workers compensation costs down? Create a warehouse safety checklist.
Put together a warehouse safety checklist with a series of tasks, activities, and educational material designed to make sure everyone on your staff is fully aware of the safety procedures in your warehouse.
Here are nine things every manager should have on their warehouse safety checklist to maximum workplace safety, maintain a safe warehouse environment, and reduce unnecessary injuries are related costs.

1. Make a List of the Areas in Your Warehouse Where the Most Common Citations Occur
OSHA is continuously updating their website with new publications on warehouse safety, complete with adoptable solutions designed for businesses to minimizes worksite injuries and reduce accidents.
Here are the top ten areas OSHA identified where the majority of workplace injuries occur:
• Forklifts
• Electrical, wiring methods
• Electrical, system design
• Hazard communication areas
• Floor and wall openings and holes
• Mechanical power transmission
• Exits
• Respiratory protection areas
• Portable fire extinguishers
• Lockout/Tagout
Keep a copy of this list and create safety protocols for each of these areas.
2. Post Safety Instructions and Expectations
If your employees don’t know what your safety expectations are, they can’t execute them.
Post visible signs with clear instructions next to all of the areas on OSHA’s top ten list - hand jacks, forklifts, floor and wall openings, etc. These signs will provide your employees constant visual cues that they’re near dangerous areas, and provide lists of safety precautions they should take to avoid workplace injuries.
By posting safety instructions, you set the expectation for your employees that safety is always a priority. Whether that means remembering to wear a hard hat or taking a wide berth around holes, posted instructions will instill mindfulness in your employees.

3. Post Emergency Signs
The moment an incident occurs is not the moment your employees should be learning how to handle that situation.
Just like with your safety instructions, you need to post signs emergency signs for:
- Emergency exits
- Eyewash stations
- First-aid kit locations
- Fire extinguisher locations
- Any other emergency equipment
Sometimes, the difference between a severe injury and a minor incident can be seconds. Make sure your employees can quickly locate any safety equipment they may need and that they know how to use it.
4. Eliminate Safety Hazards or Place Signs Around Them
(Yes, you need more signs)
Warehouses are rife with potential hazard zones. Some of them you can eliminate by doing regular safety sweeps.
Check for things like:
- ‘Slip and Trip’ hazards (stray cords or liquids)
- Loose equipment or materials
- Improperly stored equipment or materials
Also, make sure to store dangerous equipment in areas that are clearly labeled with safe walkways highlighted around the equipment. Black and white or orange stripes on the floor are the best way to designate safe walkways.
For potential hazards you can’t eliminate, like cracks or pits in the floor, there are two ways to reduce potential injuries
- Post signs around the hazard or area
- Use fall protection devices or equipment
Fall protection devices and equipment can be restraints that prevent free falls, like full body harness, warning lines, and guard or standard railings. Or, they can be fall arrest systems that stop an employee who is in the middle of a fall, like safety nets.
5. Provide Necessary Safety Equipment and Make Sure it’s Always Used
Safety equipment is designed to minimize workplace injury. Constantly reminding your employees to use it can be tedious, but it will dramatically reduce the number of injuries that occur in your warehouse.
Confirm that your warehouse has all of the following equipment and make sure your employees know where these things are, how to use them, and when to use them:
• Surge Protectors and Outlets
• Light switches
• Movable signs for slip and trip hazards
• Fire extinguishers
• Eyewash stations
• Eyewear, hardhats, and harnesses
• Alarm systems
• Restrooms and washing facilities
• Marked exits
6. Train Your Employees in Safe Lifting Techniques
When your employees need to transport a load, they should always assess the best method of transportation before attempting to move it.
If it’s decided that manually lifting the load is the best option, your employees should check that the route they’ll take is free of obstacles and has enough space to fit themselves and the load.
The load should never obstruct the view of the lifter, and safe lifting techniques should be utilized at all times. Make sure your employees know when to push rather than pull and to always lean in the direction the equipment is headed.
For loads that require the use of a forklift or similar equipment, make sure your employees are trained in its use.
7. Conduct Regular Warehouse Safety Training Sessions and Refresher Courses
Your staff should be equipped with up-to-date knowledge on warehouse safety best practices. Having proper knowledge of safety procedures will increase adherence and educate your staff on the consequences of unsafe working environments.
For example, most fatal accidents occur when employees cut safety corners to save time. When people are aware of that fact, they’re more likely to follow proper safety procedures.
Regular seminars and training sessions on workplace safety practices are the best way to guarantee your staff is educated on safety-related topics.
These types of sessions should be a requirement for all employees. If you’re having trouble getting your workers to attend safety workshops, you can offer free breakfast or lunch during the meetings to increase participation.
8. Promote Safety Awareness
The more aware your employees are of safety protocols, the more likely they are to implement them.
Communicate safety procedures and expectations as often as possible.
Have lots of employees in one area completing tasks? Make sure they’re shouting their location to one another to avoid collisions.
Carrying loads or driving machinery? Train people to shout a simple “coming through” to alert their coworkers to their location and clear pathways.
Train your staff to be vigilant and maintain constant awareness of who and what’s around them so they can communicate those things to co-workers and prevent incidents and injuries.
9. Conduct Regular Safety Sweeps
No one likes a pop quiz - except the person administering it!
Conduct daily, weekly, or monthly sweeps to troubleshoot safety hazards and make sure your employees are following proper safety protocols.
When you’re conducting your sweeps, use your warehouse safety checklist and walk around to all of OSHA’s top ten hazard locations to make sure you’ve eliminated dangers or put up proper signage and barriers.
Safety should always be a priority in the workplace. Do you have any more safety guidelines to add to our checklist? Leave recommendations in the comments section.